Sự khác biệt chính giữa PLC và DCS là gì?
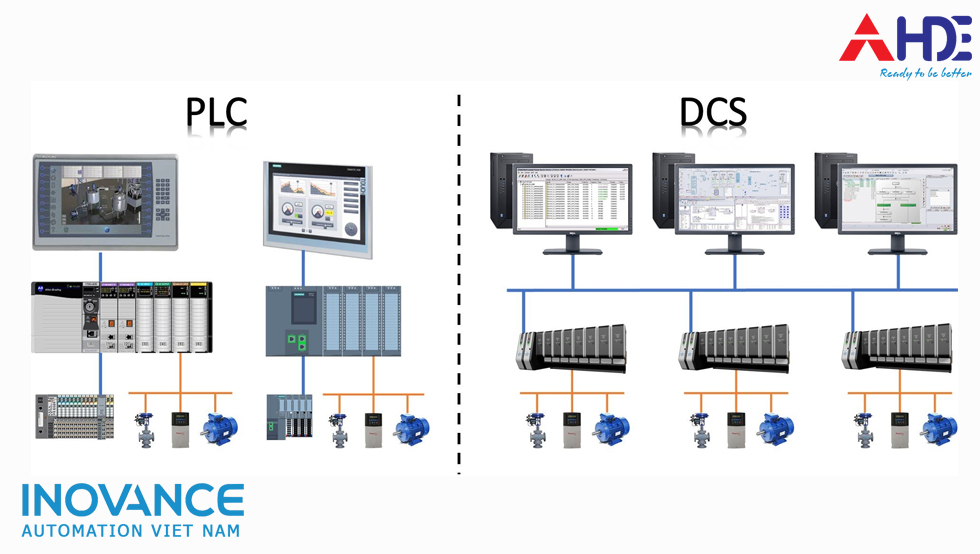
Trong lĩnh vực tự động hóa công nghiệp, PLC (Programmable Logic Controller) và DCS (Distributed Control System) là hai hệ thống điều khiển quan trọng, phổ biến nhất được sử dụng rộng rãi để tự động hóa các quy trình sản xuất. Tuy nhiên, nhiều người mới hoặc cả những người đã làm việc lâu năm trong ngành cũng thường nhầm lẫn hoặc chưa phân biệt rõ giữa hai hệ thống này. Vậy, PLC và DCS khác nhau ở điểm nào? Bài viết này sẽ giúp bạn hiểu sâu sắc về sự khác biệt chính giữa PLC và DCS cũng như ứng dụng của từng loại hệ thống trong công nghiệp.
1. Định nghĩa cơ bản về PLC và DCS
PLC là gì?
PLC (Programmable Logic Controller) hay còn gọi là bộ điều khiển logic lập trình là một thiết bị điều khiển lập trình được thiết kế để thực hiện các nhiệm vụ điều khiển theo logic trong tự động hóa công nghiệp. PLC thường được sử dụng để điều khiển các máy móc và dây chuyền sản xuất với các chức năng logic, tính toán, giám sát trạng thái đầu vào/đầu ra (I/O) nhanh và chính xác.
PLC được phát triển để thay thế các bảng mạch rơle truyền thống, giúp đơn giản hóa thiết kế hệ thống điều khiển, giảm thời gian lập trình và tăng khả năng mở rộng.
DCS là gì?
DCS (Distributed Control System) hay hệ thống điều khiển phân tán là một hệ thống điều khiển tự động hóa có kiến trúc phân tán, trong đó các chức năng điều khiển được phân phối trên nhiều bộ điều khiển riêng biệt, được kết nối qua mạng truyền thông. DCS thường được dùng trong các nhà máy công nghiệp lớn có quy trình phức tạp như lọc hóa dầu, nhà máy điện, nhà máy hóa chất, chế biến thực phẩm,…
DCS không chỉ thực hiện điều khiển mà còn tích hợp khả năng giám sát quá trình sản xuất, thu thập dữ liệu, quản lý vận hành và tối ưu hóa hệ thống.
2. So sánh sự khác biệt giữa PLC và DCS
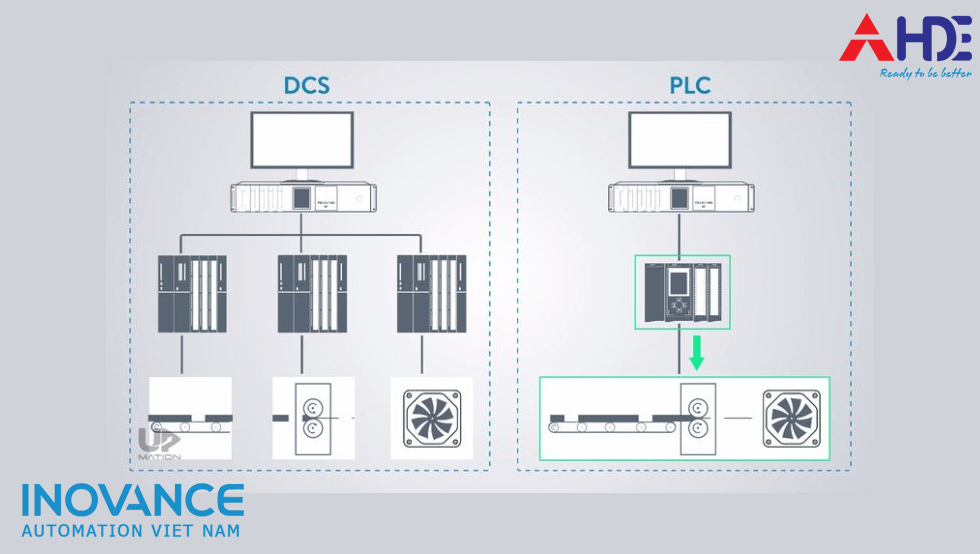
Tiêu chí | PLC | DCS |
---|---|---|
Kiến trúc hệ thống | Trung tâm – thường là hệ thống điều khiển tập trung với bộ xử lý đơn hoặc nhóm PLC riêng lẻ. | Phân tán – các bộ điều khiển nhỏ được phân bố khắp hệ thống, kết nối qua mạng truyền thông. |
Phạm vi ứng dụng | Thường dùng cho các ứng dụng điều khiển logic, máy móc riêng lẻ, dây chuyền sản xuất nhỏ và vừa. | Dùng cho các quy trình công nghiệp lớn, phức tạp, cần điều khiển liên tục và giám sát tổng thể. |
Khả năng mở rộng | Mở rộng bằng cách thêm các mô-đun I/O hoặc thêm PLC khác. | Mở rộng dễ dàng bằng cách bổ sung các bộ điều khiển phân tán và các trạm mạng. |
Xử lý tín hiệu | Xử lý tín hiệu kỹ thuật số và tương tự; tốc độ xử lý rất nhanh. | Xử lý tín hiệu tương tự và kỹ thuật số; thường ưu tiên ổn định và an toàn hơn tốc độ. |
Giao diện người dùng | Thường dùng HMI (Human Machine Interface) riêng biệt hoặc thông qua phần mềm lập trình. | Hệ thống SCADA tích hợp giao diện điều khiển và giám sát toàn bộ quá trình. |
Độ tin cậy | Tốt, phù hợp ứng dụng quy mô nhỏ đến vừa. | Rất cao, phù hợp với ứng dụng yêu cầu độ ổn định và an toàn tuyệt đối. |
Khả năng xử lý lỗi | Xử lý lỗi chủ yếu tại chỗ, có thể cần can thiệp thủ công. | Tự động phát hiện, báo cáo và xử lý lỗi theo quy trình nghiêm ngặt. |
Chi phí đầu tư | Thấp hơn, phù hợp doanh nghiệp nhỏ và vừa. | Cao hơn, phù hợp nhà máy công nghiệp lớn với quy trình phức tạp. |
3. Chi tiết sự khác biệt chính giữa PLC và DCS
3.1. Kiến trúc và cấu trúc hệ thống
-
PLC có kiến trúc tập trung hoặc phân tán nhưng quy mô nhỏ. Các bộ PLC có thể hoạt động độc lập hoặc kết nối với nhau qua mạng nhỏ. Các PLC thường có kích thước nhỏ gọn, dễ dàng cài đặt tại chỗ và lập trình.
-
DCS có kiến trúc phân tán hoàn chỉnh, mỗi bộ điều khiển chịu trách nhiệm một phần riêng biệt của quá trình, được liên kết qua mạng truyền thông công nghiệp tốc độ cao. Hệ thống này giúp tối ưu hóa việc phân bố chức năng và tăng độ tin cậy hệ thống.
3.2. Phạm vi và ứng dụng
-
PLC chủ yếu dùng cho điều khiển tuần tự, logic trong các máy móc, thiết bị riêng lẻ hoặc dây chuyền tự động nhỏ và vừa. Ví dụ: điều khiển băng tải, máy đóng gói, hệ thống cấp liệu tự động,…
-
DCS được ứng dụng trong các nhà máy lớn, quy trình liên tục hoặc phức tạp, đòi hỏi sự giám sát toàn diện và điều khiển chính xác từng bước trong quy trình. Ví dụ: nhà máy lọc dầu, nhà máy nhiệt điện, nhà máy hóa chất,…
3.3. Tốc độ xử lý và tính năng điều khiển
-
PLC thường có tốc độ xử lý cực nhanh, có thể xử lý các tín hiệu digital và analog rất chính xác, phù hợp cho các ứng dụng yêu cầu phản hồi nhanh và thời gian thực.
-
DCS tập trung nhiều vào độ ổn định và an toàn trong điều khiển, tốc độ xử lý tuy không nhanh bằng PLC nhưng lại tối ưu cho việc quản lý các quy trình phức tạp, liên tục.
3.4. Khả năng mở rộng và linh hoạt
-
PLC có thể mở rộng bằng cách thêm mô-đun đầu vào/đầu ra hoặc thêm nhiều bộ PLC khác. Việc mở rộng này phù hợp cho các hệ thống nhỏ đến vừa.
-
DCS cho phép mở rộng dễ dàng hơn rất nhiều nhờ kiến trúc phân tán, chỉ cần bổ sung các trạm điều khiển hoặc các node trên mạng. Điều này giúp hệ thống có thể phát triển linh hoạt theo quy mô nhà máy.
3.5. Giao diện người dùng và phần mềm
-
PLC thường đi kèm với các phần mềm lập trình riêng biệt. Người vận hành dùng HMI để giám sát và điều khiển từng thiết bị.
-
DCS tích hợp giao diện SCADA mạnh mẽ, cho phép giám sát toàn bộ hệ thống sản xuất trên một nền tảng thống nhất, cung cấp dữ liệu chi tiết và khả năng phân tích.
3.6. Độ tin cậy và bảo mật
-
PLC có độ tin cậy cao trong các ứng dụng công nghiệp nhưng thường phù hợp cho các hệ thống quy mô nhỏ và vừa.
-
DCS có độ tin cậy và khả năng bảo mật cao hơn, đặc biệt phù hợp cho các nhà máy yêu cầu vận hành liên tục và an toàn như trong ngành năng lượng, hóa chất.
4. Ưu điểm và nhược điểm của PLC và DCS
4.1. Ưu điểm của PLC
-
Thiết kế đơn giản, dễ lập trình và vận hành.
-
Chi phí đầu tư ban đầu thấp hơn so với DCS.
-
Tốc độ xử lý nhanh, phù hợp các ứng dụng yêu cầu phản hồi tức thời.
-
Linh hoạt trong việc mở rộng hệ thống cho các quy mô nhỏ và vừa.
-
Đa dạng nhà sản xuất và giải pháp cho nhiều ứng dụng khác nhau.
4.2. Nhược điểm của PLC
-
Hạn chế trong việc quản lý và giám sát hệ thống quy mô lớn.
-
Khó khăn khi tích hợp với các hệ thống SCADA phức tạp.
-
Không phù hợp với quy trình liên tục hoặc phức tạp cao.
4.3. Ưu điểm của DCS
-
Kiến trúc phân tán giúp tăng độ tin cậy và khả năng phục hồi.
-
Giám sát và điều khiển toàn diện cho hệ thống quy mô lớn.
-
Tích hợp dễ dàng với hệ thống SCADA và các phần mềm quản lý vận hành.
-
Hỗ trợ điều khiển liên tục và phức tạp, phù hợp các ngành công nghiệp lớn.
-
An toàn và bảo mật cao.
4.4. Nhược điểm của DCS
-
Chi phí đầu tư ban đầu và chi phí bảo trì cao hơn PLC.
-
Yêu cầu kỹ thuật vận hành và bảo trì phức tạp hơn.
-
Ít linh hoạt khi thay đổi hoặc mở rộng quy mô nhỏ.
5. Ứng dụng thực tế của PLC và DCS
5.1. Ứng dụng PLC
-
Dây chuyền lắp ráp ô tô.
-
Hệ thống đóng gói thực phẩm.
-
Máy móc sản xuất bao bì.
-
Tự động hóa nhà máy nhỏ và vừa.
-
Hệ thống băng tải, máy ép nhựa, máy CNC.
5.2. Ứng dụng DCS
-
Nhà máy lọc dầu.
-
Nhà máy sản xuất điện.
-
Nhà máy hóa chất và dược phẩm.
-
Nhà máy sản xuất xi măng quy mô lớn.
-
Hệ thống xử lý nước thải quy mô công nghiệp.
6. Khi nào nên chọn PLC, khi nào nên chọn DCS?
6.1. Nên chọn PLC khi:
-
Hệ thống có quy mô nhỏ hoặc vừa, yêu cầu điều khiển logic tuần tự.
-
Cần tốc độ xử lý nhanh, phản hồi thời gian thực.
-
Chi phí đầu tư và vận hành hạn chế.
-
Hệ thống đơn giản, ít cần giám sát tổng thể phức tạp.
6.2. Nên chọn DCS khi:
-
Nhà máy có quy mô lớn, quy trình phức tạp, cần điều khiển liên tục.
-
Yêu cầu giám sát và quản lý toàn bộ hệ thống chặt chẽ.
-
Cần khả năng bảo mật và an toàn cao.
-
Mục tiêu tối ưu hóa vận hành, giảm thiểu sự cố và downtime.
7. Tổng kết
PLC và DCS là hai hệ thống điều khiển tự động hóa công nghiệp không thể thay thế nhau hoàn toàn mà bổ sung cho nhau trong các ứng dụng khác nhau. Việc lựa chọn giữa PLC và DCS phụ thuộc vào quy mô, tính chất quy trình, yêu cầu về hiệu suất và ngân sách của doanh nghiệp.
Hiểu rõ sự khác biệt giữa PLC và DCS giúp doanh nghiệp đưa ra quyết định phù hợp, tối ưu hóa hiệu quả vận hành và nâng cao năng suất trong sản xuất. Nếu bạn cần tư vấn hoặc giải pháp tự động hóa, hãy liên hệ các chuyên gia trong ngành để được hỗ trợ tốt nhất.
8. Mua PLC và DCS chất lượng tại Công ty Cổ phần Điện Hải Dương (HDE)
Nếu bạn đang tìm kiếm các giải pháp PLC và DCS uy tín, chất lượng cao cho hệ thống tự động hóa của doanh nghiệp, Công ty Cổ phần Điện Hải Dương (HDE) chính là địa chỉ tin cậy dành cho bạn. Với nhiều năm kinh nghiệm trong lĩnh vực cung cấp và tích hợp các thiết bị tự động hóa, HDE cam kết mang đến sản phẩm chính hãng từ các thương hiệu hàng đầu như Siemens, Mitsubishi, Allen Bradley, ABB, Schneider Electric, Yokogawa, Honeywell và nhiều nhà sản xuất uy tín khác.
Tại HDE, bạn sẽ nhận được:
-
Tư vấn chuyên sâu từ đội ngũ kỹ sư giàu kinh nghiệm để lựa chọn thiết bị phù hợp nhất với nhu cầu và quy mô hệ thống của bạn.
-
Giải pháp thiết kế và tích hợp hệ thống tự động hóa toàn diện, giúp tối ưu hóa vận hành và giảm thiểu chi phí sản xuất.
-
Dịch vụ lắp đặt, bảo trì và hỗ trợ kỹ thuật tận tâm, đảm bảo hệ thống hoạt động ổn định và hiệu quả lâu dài.
-
Chính sách bảo hành rõ ràng và minh bạch, tạo sự an tâm tuyệt đối cho khách hàng khi đầu tư vào thiết bị.
Với sự đa dạng về sản phẩm và dịch vụ chuyên nghiệp, HDE là đối tác tin cậy giúp bạn xây dựng hệ thống tự động hóa hiện đại, đáp ứng tốt nhất yêu cầu sản xuất và nâng cao năng lực cạnh tranh trên thị trường.
Thông tin liên hệ:
-
Hotline: 0978.093.697
——
Liên hệ tư vấn các thiết bị miễn phí theo Hotline: 0978.093.697
Facebook: Công Ty CP Điện Hải Dương – HDE
Youtube: HDE Tech
Tiktok: HDE Tech